Производња амонијака
Данас је азијска индустрија једна од водећихиндустрије. Употреба амонијака проширила се на расхладну опрему (Р717, расхладно средство), медицину (раствор амонијака или алкохол алкохола), пољопривреда (ђубрива).
Примарна пажња посвећена је производњи азотних ђубрива (а самим тим и њиховим базама, укључујући и амонијак, чија потражња је порасла за 20% у посљедње двије деценије).
Али производња амонијака разликује се, пре свега, високим енергетским интензитетом. Цела историја ове производње је борба за снижавање коришћене енергије (механичке, термичке, електричне).
Синтеза амонијака открива формулу:
Н2 + 3Х2 = 2НХ3 + К
Реакција је егзотермна, реверзибилна, са смањењемзапремине. Пошто је реакција егзотермна, смањење температуре помјериће равнотежу у формирање амонијака, међутим, брзина реакције ће се значајно смањити. Производња амонијака треба да иде на високим температурама (синтеза се одвија на 500 степени Целзијуса). Повећање т ће довести до реверзне реакције. Притисак од 15 до 100 МПа омогућава избјегавање утицаја температуре (ниског притиска - од 10 до 15 МПа, просјечног притиска - од 25 до 30 МПа, високог притиска - изнад 50 МПа). Од ових, просек је пожељнији.
Катализатор је гвожђе спужве са адитиви калцијума, силикона, калијума, алуминијум оксида.
Штетне нечистоће (угљен моноксид, вода,водоник сулфид) негативно утичу на брзину реакције реакције, тровајући катализатор, чиме се смањује његова активност и смањује животни век. То значи да се мешавина водоник-сулфида мора обавезно темељито очистити. Али и након пречишћавања, само део ове смеше претвара у амонијак. Према томе, преостала неизлечена фракција се поново шаље у реактор.
Како се производи амонијак?
Цевовод се испоручује са већ припремљеном мешавиномтри дела водоника и један азот. Прође кроз турбопуњач, где се компримује до горе наведеног притиска и шаље се у синтезну колону с катализатором на уграђене полице. Процес, како смо сазнали, је врло егзотермичан. Смеша нитро-водоник се загрева кроз развијену топлоту. Око 25 процената амонијака и нереагираног азота са водоником излазе из колоне. Цијели састав се пуни у фрижидер, где се смеша охлади. Амонијак под притиском постаје течност. Сада се уђе у сепаратор, чији задатак је да одвоји амонијак у колекцију на дну и непрописану смешу, коју циркулациона пумпа враћа назад у колону. Због овог циркулације, мешавина нитро-водоника користи 95 процената. Течни амонијак кроз цевовод амонијака иде у посебан складиште.
Сви уређаји који се користе у производњи,максимално херметичко, што елиминише цурење. Користи се само енергија ексотермних реакција. Шема је затворена, ниско отпада. Трошкови се смањују кроз континуирани и аутоматизовани процес.
Производња амонијака не може утицатиокружење. Емисије гаса су неизбежне, укључујући амонијак, угљеник и азотне оксиде и друге нечистоће. Отпуштена је ниска температура. Вода се одбацује након прања система хлађења и самог реактора.
Због тога је производња амонијакаукључују каталитичко чишћење с средством за смањење гаса. Смањивање количине отпадних вода може се постићи замјеном компресора клипа са турбо пуњачима. Низак потенцијал топлоте може се искористити увођењем топлоте високог потенцијала. Међутим, ово ће повећати загађење димним гасовима.
Енергетско-технолошка шема која обухвата циклус комбинованог циклуса где се користе и парна топлота и производи сагоревања истовремено ће повећати ефикасност производње и смањити емисије.
</ п>



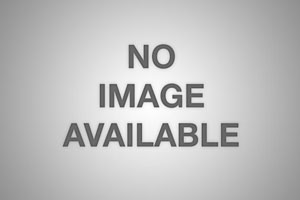
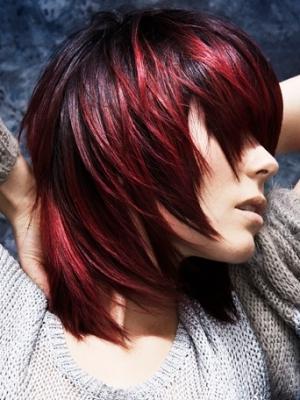
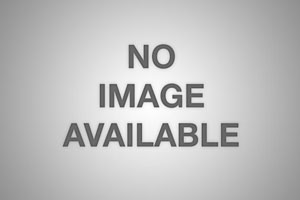
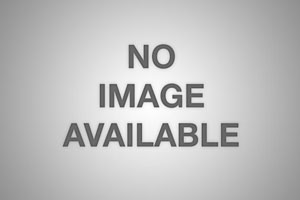
